Pregis' PolyPlank Plus Combines Adhesive, Lamination To Create New Generation Of Cost-Effective Foam Plank
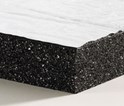
Deerfield, IL - New PolyPlank Plus from Pregis Corp. combines various substrates and two-step lamination technology to create a new generation of cost-effective protective foam plank products.
The outer layer of PolyPlank Plus can be made from a broad variety of substrates such as foil, paper, air cushioning, nonwovens, scrims, adhesive and cohesive films, etc.
In the first step, the substrate is laminated onto an engineered foam sheet. This assembly is then laminated to a thicker single or multilayer plank structure. For example, you can laminate a pressure-sensitive adhesive layer to PolyPlank Plus. This creates a custom foam block that, when adhered to a product, protects surfaces from punishing impact without marring finishes or leaving residue.
Packagers need only remove the release liner to expose the adhesive and adhere the adhesive or cohesive/protective foam block to the product or packaging surface. (The plank lamination can also be manufactured without an adhesive layer for those applications which do not require it.)
By removing a fabrication step, PolyPlank Plus gives packagers a cost-effective alternative to traditional custom fabricated foam plank cushioning.
"For example, end caps for computer towers traditionally have been custom-fabricated to fit around the edges. This custom fabrication adds another step and, as a result, adds to packaging costs. Because PolyPlank Plus has been engineered to adhere directly to the component or packaging surface, custom fabrication is no longer necessary. You can simply cut the foam plank into various sized blocks, expose the adhesive and adhere the piece directly onto the desired surface," explains Tony Smith, general manager, engineered products, Pregis.
PolyPlank Plus is ideal for applications such as industrial parts, appliances, aircraft components, marine parts, industrial equipment, furniture and consumer electronics—any item with a painted or non-painted surface that needs to be protected during shipment.
The wide variety of substrates available also opens the door to innovative applications. For example, a foil laminated plank can be used in a corrugated shipper to help transport lobsters "on ice" and other seafood items. Non-woven material can be laminated to foam to improve non-abrasive qualities. Scrim and/or other materials can be added to improve tear and puncture resistance for objects with sharp edges. Films can be utilized to improve the strength of living hinge end-caps or corner protectors.
"Manufacturers are constantly looking for ways to minimize packaging costs while still protecting their products in transit. We believe that PolyPlank Plus offers many high-performance protection options which may not currently exist in the marketplace or which may be too costly to produce at the fabricator level." says Smith. PolyPlank Plus is made from closed-cell polyethylene foam and provides superior protection against shock and vibration during transport. It can be made up to 48-inches wide, in thicknesses ranging from 1- to 10-inches in most densities.
SOURCE: Pregis Corp.